Dust Collection System Considerations – Part 2
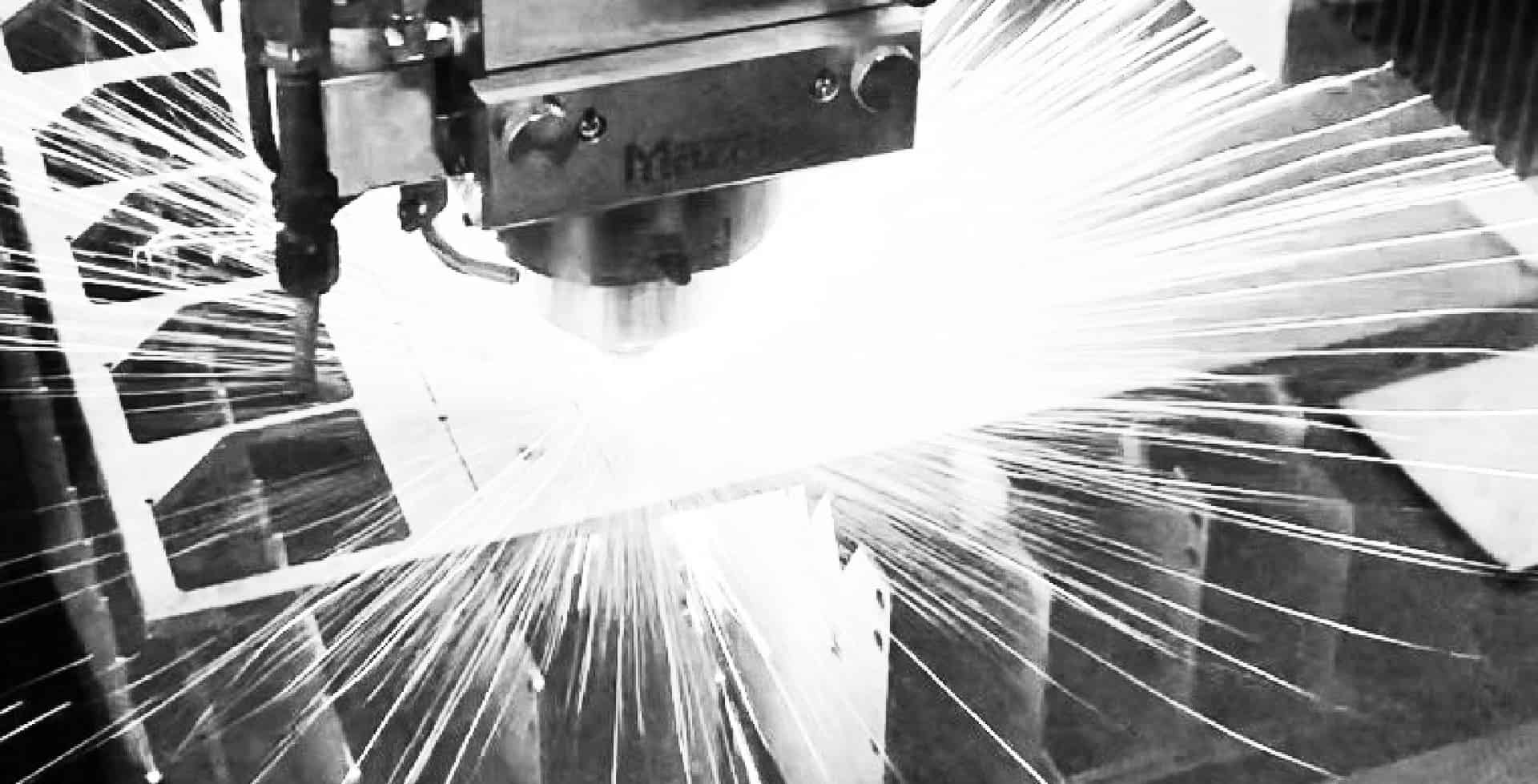
Construction, Start-Up, Training & Maintenance Phases
Building and Managing a Dust Collection System
Many factors affect the performance of Dust Collection Systems. In a previous blog post, Dust Collection System Design Considerations – Part 1, we summarized five key considerations for the engineering and design phase of a dust collection system. The post was based on an Engineers Collaborative article, Guidelines for Operating and Maintaining Industrial Dust Control Exhaust Systems (Unfortunately, this is now only available via the Internet Archive.)
For this post, we return to that article to summarize its advice for managing the following phases of a dust collection project:
- Construction
- Startup
- Training
- Maintenance
The Construction Phase
Appropriately detailed engineering and design documents produced in the design phase help ensure the construction phase meets design intent, reducing future operating and maintenance problems.
During the construction phase, you should:
- Conduct fabrication checks: Inspect components for proper construction and gauge as they are being made, not just before they are shipped.
- Inspect the ventilation and exhaust system:
- Make sure components do not block access to each other or to other plant services and equipment.
- Repair or replace components damaged during shipping or installation.
- Protect dust collector filters from weather and construction activities.
- Before startup, ensure your ventilation or exhaust system satisfies engineering and design documents.
The Start-Up Phase
These elements need to be validated at startup:
- Airflow in the duct system: The dust capture hoods should exhaust the designed air quantities, according to standards in the Industrial Ventilation Manual published by the American Conference of Governmental Industrial Hygienists. The data collected during this air system balancing becomes the project’s baseline information.
- Industrial ventilation system safety components: Check that fire and explosion protection components, pressure gauges, and low-flow and over-pressure alarm systems are set up as intended in the engineering and design documents.
- Component baseline documentation: Record baseline information for all other system components, including dust capture hood static, dust collector and safety monitoring filter system (HEPA) static pressures, and main duct velocity pressure to ensure it complies with the level recorded in your state permit application.
- Industrial hygiene particulate air sampling: Monitor air for particulates to ensure that dust sources are controlled to the desired level. Make modifications to the dust control system components as needed and then update component baseline documentation.
Staff Training
Plant supervisory, production and maintenance personnel should be trained in the following areas:
- Safety features and components
- Air meter read-outs and alarms
- Baseline documentation for components
- Operating and maintenance instructions and recommendations
- Operation and use of dust capture hoods and dampers
- Preventive maintenance
Preventative Maintenance Activities
Component repair activities include greasing fan bearings and emptying dust collector hoppers on schedule, replacing obsolete dust capture hoods and ductwork, and repairing damaged dust control system components. However, these and other component repair activities should be supported by four critical activities:
1. Check system operating characteristics: Periodically inspect the system visually and ensure components’ operating characteristics, such as static and velocity pressures, meet standards set during the start-up phase. Analyze and correct any deviations.
2. Inspect explosion protection components: Inspect explosion relief or suppression systems to ensure they comply with manufacturers’ recommendations and applicable safety guidelines.
3. Consider the effect of product changes: Include maintenance personnel in new product discussions as changes to the processed dust can affect the dust control exhaust system’s performance.
4. Sample air for particulates: Periodic air sampling should be performed to ensure the dust control system is meeting standards set during the start-up phase. Investigate any deviations you find.
IVI performs all aspects related to the construction, start-up, training and maintenance of industrial ventilation systems to ensure customized dust collection systems operate at optimal performance.
Contact us for more information.